With the increasing requirements for clean steel in various industries and the development of continuous casting technology, the metallurgical function of the tundish between the ladle and the crystallizer has received more and more attention. Tundish metallurgy can prevent secondary oxidation of molten steel, improve the flow state of molten steel, prevent slag rolling and promote the floating of inclusions, control the morphology of inclusions and accurately control the superheat of molten steel, which plays an important role in improving the continuous casting ratio and improving steel quality.
By installing retaining walls, dams, turbulence controllers, filters and air-permeable bricks and their combined devices in the tundish as devices to control the flow state of molten steel, it is beneficial to remove inclusions. The upper retaining wall, or slag weir, is installed across the entire width of the tundish, extending from above the molten steel surface to a certain distance from the bottom of the tundish, allowing molten steel to pass from below. It can control the size of the impact area, promote small-sized inclusions to collide with each other and aggregate into large inclusions, which are easier to float and be absorbed and removed by the slag layer. The upper retaining wall can also isolate the ladle slag that enters the tundish with the ladle injection in the impact area, thereby reducing the secondary contamination of molten steel caused by ladle slag rolling. At the same time, the upper retaining wall stabilizes the downstream molten steel level and reduces the number of inclusions caused by secondary oxidation and mechanical scouring. The dam, or lower retaining wall, is also installed across the entire width of the tundish, extending from the bottom of the tundish upward to a certain distance below the molten steel surface, and the molten steel passes over it. The functions of the lower retaining wall include: extending the flow path of the molten steel, increasing the residence time, and preventing the formation of short-circuit flow; as well as shortening the floating distance of inclusions, further promoting the floating of inclusions, and purifying the molten steel. The upper and lower retaining walls are usually used in combination in the tundish to obtain the ideal tundish metallurgical effect.
Most of the inclusions in molten steel are oxide inclusions and refractory materials are also mainly oxides. Therefore, testing the total oxygen content in molten steel is an important indicator for evaluating the cleanliness of molten steel. Consistent with the thermodynamic calculation of the oxygenation of molten steel by oxides, the total oxygen content of molten steel introduced by magnesium or magnesium-calcium materials is low, while silicon or high-aluminum materials significantly increase the oxygenation of molten steel. From the perspective of improving the cleanliness of molten steel, magnesium refractory materials are often used in parts that are in long-term contact with molten steel, such as the working lining of the tundish (wall) and retaining wall. The working lining material is currently mainly magnesium coating material or dry material, while retaining walls and dams use magnesium castables.
Magnesium coatings add a high content of water to ensure construction, which will cause hydration problems. Magnesium oxide reacts with water or water vapor to form magnesium hydroxide. The reaction is accompanied by a volume expansion of about 1.5 times, which will cause cracks during the curing and baking stages, and the steel pouring process is prone to peeling or collapse. If the moisture in the coating is not completely removed during the baking stage, the decomposition of the residual water will cause the molten steel to increase [H]. Compared with the coating, dry materials are a type of amorphous refractory material that is constructed in a water-free state by vibration molding. It has the advantages of short baking time, fast heating rate and easy detachment. Magnesium dry materials use organic binders such as phenolic resin, asphalt and rosin, which decompose at temperatures below 1000°C, thereby affecting the medium and high temperature bonding strength of the material; in addition, the decomposition of organic binders poses the risk of increasing [C] and [H] to the molten steel, affecting the quality of the molten steel. At the same time, inorganic binders such as polyphosphates and sodium metasilicate have also been developed. Polyphosphate binders still have the problem of increasing [P]. When sodium metasilicate is used as a binder, it gradually melts during the heating process, so that the surface of the magnesia particles is coated with liquid inorganic salts. The magnesia aggregate and the matrix can be fully bonded to form a combination with a certain strength, ensuring good medium and low temperature strength of the dry material, while reducing the problem of increasing [C], [H], [S] and [P] in the molten steel.
Compared with the working lining, the flow control device is more exposed to the continuous scouring of molten steel and has higher requirements for material strength. Therefore, magnesium castables or prefabricated parts are generally used. In addition, the upper retaining wall is also subject to slag erosion, and the magnesium castable is also required to have good slag erosion resistance. The chemical composition of magnesium castables is mainly magnesium oxide, silicon oxide and aluminum oxide. Silicon oxide has a strong ability to increase oxygen in molten steel and increases the oxygen concentration. It is easy to undergo oxidation-reduction reactions with metal elements in steel to form oxide inclusions (as shown in equations 1 to 3), which reduces the cleanliness of the molten steel.
3SiO2+4[Al]→[Si]+2Al2O3 (1)
SiO2+2[Mn]→[Si]+2MnO (2)
SiO2+[Ti]→[Si]+TiO2 (3)
Since P2O5 and CaO can form a stable compound C2L4P2O9 and S reacts with CaO to form CaS, magnesium-calcium materials containing free calcium oxide are more effective in removing [S] and [P] from steel than castables made of other materials. Tao Shaoping’s research also pointed out that although magnesium-aluminum refractory materials (MgO>82wt%) have limited effects on purifying molten steel, they do not pollute molten steel; however, aluminum-magnesium refractory materials (MgO<14wt%) cannot remove inclusions in steel and may also melt into the molten steel, increasing the number of inclusions. Therefore, from the perspective of molten steel cleanliness, while ensuring the basic physical properties of magnesium castables, the amount of silicon oxide and aluminum oxide added in the composition should be reduced as much as possible.
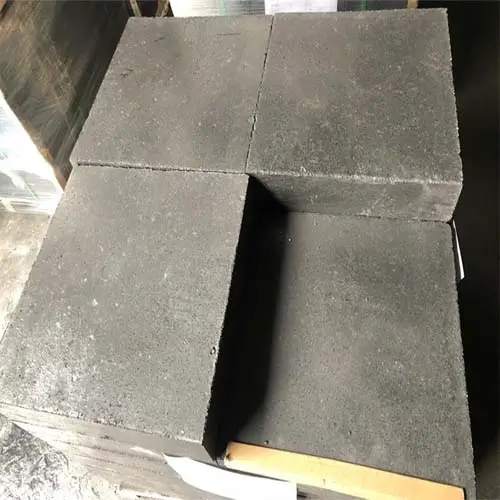